Studio Page: process………….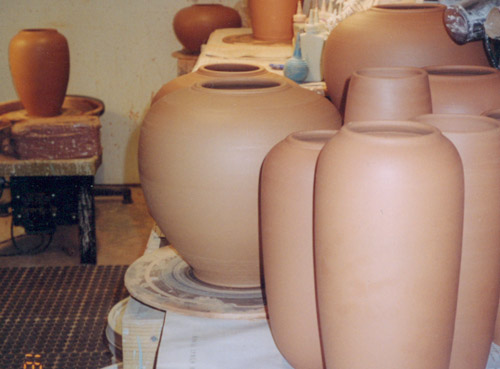
All of my work is hand-thrown on a potter’s wheel using stoneware claybodies of various colors. The raised decoration is achieved by using a porcelain clay slip (liquid clay) the consistency of thick cream. I use natural powdered oxides and commercial stains for color and apply the slip using brushes and squeeze bottles. This is done while the piece is still damp or “leather hard.” In this way the decoration becomes one with the pot. My shelves are usually full of many forms covered in plastic, waiting for decoration. The trick is keeping them damp enough. My spray bottle is my friend!
After pieces are decorated and completely dry they are “bisque fired” (partially fired) so the surface is still porous but the pot can be handled without breaking. I carefully brush a liquid wax on all areas NOT to be glazed and immerse the pot into a vat of clear glaze. The wax will burn away, leaving the stoneware exposed, and the glaze will allow the colors of the decoration to show through.
My firing is done in a gas kiln to about 2300 degrees Fahrenheit (cone 10). A reduction atmosphere is created in the kiln by partially closing the damper during the end of the firing. This gives the unglazed stoneware its rich toasty color.
All pieces are watertight and food safe, even on the unglazed areas. They are also safe for the dishwasher and microwave.